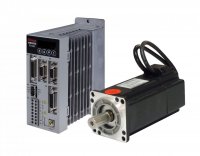
In industry, a trend is clearly visible to produce faster, better and, of course, cheaper. In response to these needs, manufacturers are trying to provide increasingly accurate, dynamic and at the same time attractive devices. The growing popularity of, among others, servo drives used in many different applications.
The servo drive is an executive system operating in the closed loop of the feedback loop, consisting of the motor, controller and encoder. High-performance servomotors from Kinco offered by WObit are brushless synchronous motors with alternating magnets mounted on the rotor. The use of high quality magnets allowed for a significant reduction in the dimensions and weight of the engine, while maintaining the same power. These drives are characterized by high efficiency, which remains constant in a large load range, and can also achieve high angular acceleration of the rotor. It also has good dynamic and regulatory properties, because for permanent magnet motors, a quick response to control system commands due to the relatively low moment of inertia is right. The cost of running this type of engine is low due to the lack of mechanical (fast-wearing) brushes, as well as extended lubrication periods of the bearings.
When choosing servo drive , first of all, you need to determine the engine power, and in fact its torque. Next, take into account the speed you want to achieve and the dynamics of the system: the acceleration time, braking time, the steepness of the work characteristics. In many applications, the degree of motor IP, cooling method and controller network interfaces are also important.
WObit proposes eight series of servo motors with flange sizes from 40 to 180 mm. The nominal torque range is from 0.64 Nm up to 28 Nm. All servo motors have a built-in incremental encoder with a resolution of 2500 imp / turn.. Available engine power, depending on the series, is from 200 W to 4.40 KW. An important feature that characterizes the Kinco servo drives is also the high class of thermal insulation F, allowing free operation of drives up to 155 ° C. In addition, all Kinco servo motors can be equipped with an electromagnetic brake.
An inherent and very important element of the servo drive is the servo driver , which allows you to get the required the effect of, for example, the right position, number of turns or speed. Kinco offers three series of controllers with wide possibilities and attractive price.
The basic FD series , which replaced the CD series, is intended for the control of three-phase motors servo powered by alternating current. The controllers communicate via the RS232, RS485 (Modbus RTU) and CANopen interface, thanks to which they can communicate with the PLC or the operator panel. The controllers can work in several modes: step / direction (analogous to stepper motors), speed control, torque, position, travel to the desired end position. | ![]() |
The start and stop times for the servo drives of this series are 10 ms. This allows you to set a very steep work ramp. FD series is perfect for less advanced applications for which functions are offered they are enough, while maintaining a very favorable price.
For more advanced applications, the ED series is designed, which is additionally equipped with a Profibus DP interface. The system is assembled from one or more master devices and from one or more subordinate devices and allows real-time operation of up to 127 controllers. In addition to digital inputs and outputs, ED controllers also have analog inputs and outputs. Compared to the FD series, ED controllers have a built-in timer, comparator and calculator, which also allows triggering of pre-programmed sequences of actions.
The most technically advanced series of controllers offered by Kinco is the JD series , which it is suitable for applications eg in multi-axis applications. Just like the controllers from the ED series, they can communicate via RS232, RS485 and CANopen interfaces. The JD series controllers are also equipped with the STO (Safe Torque Off) function, which ensures greater operational safety by entering the state of the engine torque block (safe torque off) in order to stop the drive. These devices are also extremely resistant to external interference and have isolation of communication interfaces. For all Kinco servo controllers, there is a PC program that includes an oscilloscope function that allows you to control parameters such as speed, position and current, and present them on a PC.
One example of applications in which the Kinco servo was used was the welding of a welding turntable. The device has been used two engines SMH60S fitted with a 400 W brake and a rated torque of 1.27 Nm. FD422-LA-00 controllers were used to control the drives.
![]() | A PLC controller cooperating with a welding robot is also used in the turntable. The robot is sent position information to one of eight outputs, which the PLC then sends to the servo controller in binary form. The controller can be set to 8 items, while the application also uses MT4414T operator panel , in which it is possible to set many programs with various drive positions and trajectories. |
Servo drives are used in many processes in which significant is to ensure the correct positions adopted by the mechanisms, such as the control of the turntable, applications of transferring and stacking products, or maintaining a constant tension of unwound or coiled material. By using servo drives it is possible to precisely control the work of the axes, by controlling the position, speed and torque. Dynamic operation and precise position control enable accurate trajectory trajectory between two end points, used for example when shaping and machining surface edges. You can read more about the applications and technical details at www.wobit.com.pl .